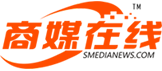
2020-06-19 23:01:57 sunmedia 590
3月6日,兰州石化公司炼油厂催化二联合车间300万吨/年重油催化裂化装置技术员马明亮仔细观察数据后,在记录本上详细记录了反再系统运行情况以及烟气中二氧化硫、粉尘、氮氧化物等污染物的含量。
“氮氧化物含量完全符合国家要求,烟气排放达标。”马明亮说,这样的监测,从300万吨/年重油催化裂化装置烟气脱硝剂工业试验启动后,每天都在进行。
2015年1月1日,新修订的《中华人民共和国环境保护法》被称为“史上最严”的环保法,去年进入工业试验阶段的300万吨/年重油催化裂化装置面临全新挑战:2014年12月底之前,排放烟气中的氮氧化物含量必须控制在240毫克/立方米以下。如果不能在国家规定期限内实现氮氧化物排放达标,装置就不能继续进行工业试验。然而,在短时间内完成氮氧化物达标排放的任务并不容易。新建环保装置,从调研、申报、建设到投用要经历一个比较长的周期,除此之外,氮氧化物减排手段非常有限。为此,兰州石化对国内外炼厂降低烟气中氮氧化物含量的方法进行了全面调研。
“目前,国内外降低催化烟气中氮氧化物含量的主要方法有烟气洗涤、原料油加氢脱硫脱氮及采用添加FPDN降氮助剂等技术。”炼油厂副厂长兼安全总监马力飞说,考虑到300万吨/年重油催化裂化装置场地受限时间紧迫,他们决定采用不需要改变装置设备结构,投资少、使用方便的添加FPDN降氮助剂方法。
研究院先在实验室内进行前期小试,小试成功的基础上进行工业放大试验。
2014年10月8日至14日,300万吨/年重油催化裂化装置进行了烟气脱硝助剂工业试验的空白标定。整个工业试验分为加速加注、稳定加注、优化加注3个阶段,历时3个月。
试验中遇到了困难。300万吨/年重油催化裂化装置再生系统属于贫氧状态。而之前的成功案例大多是在富氧再生系统条件下完成的,工业试验中,FPDN降氮助剂加注后,装置出现了明显的“不适应”症状。
“一氧化碳生成被抑制,对装置余热炉的运行造成了较大的影响。”炼油厂催化二联合车间副主任许世龙说。
兰州石化炼油厂相关部门、催化二联合车间进一步抽调精兵强将投入工业试验中,反复摸索、研究实验数据,并对FPDN降氮助剂加注量及配方进行调整。最终,第二批试剂投入使用后,彻底解决了一氧化碳生成被抑制的问题,使工业试验按计划顺利进行。截至今年2月底,在装置满负荷生产工况下,通过持续加注脱硝剂,300万吨/年重油催化裂化装置出口烟气中氮氧化物含量降低并稳定在100毫克/立方米至150毫克/立方米,达到了工业试验烟气氮氧化物含量降低目标值,优于国家标准。
本文由上海家耐磁力泵厂(https://www.shcilibeng.com)转载发布,本厂专业生产高温磁力泵、高压磁力泵、高温高压磁力泵、氟塑料磁力泵等。销售咨询技术热线:02164096960 ;13601667253。